Blasting Techniques
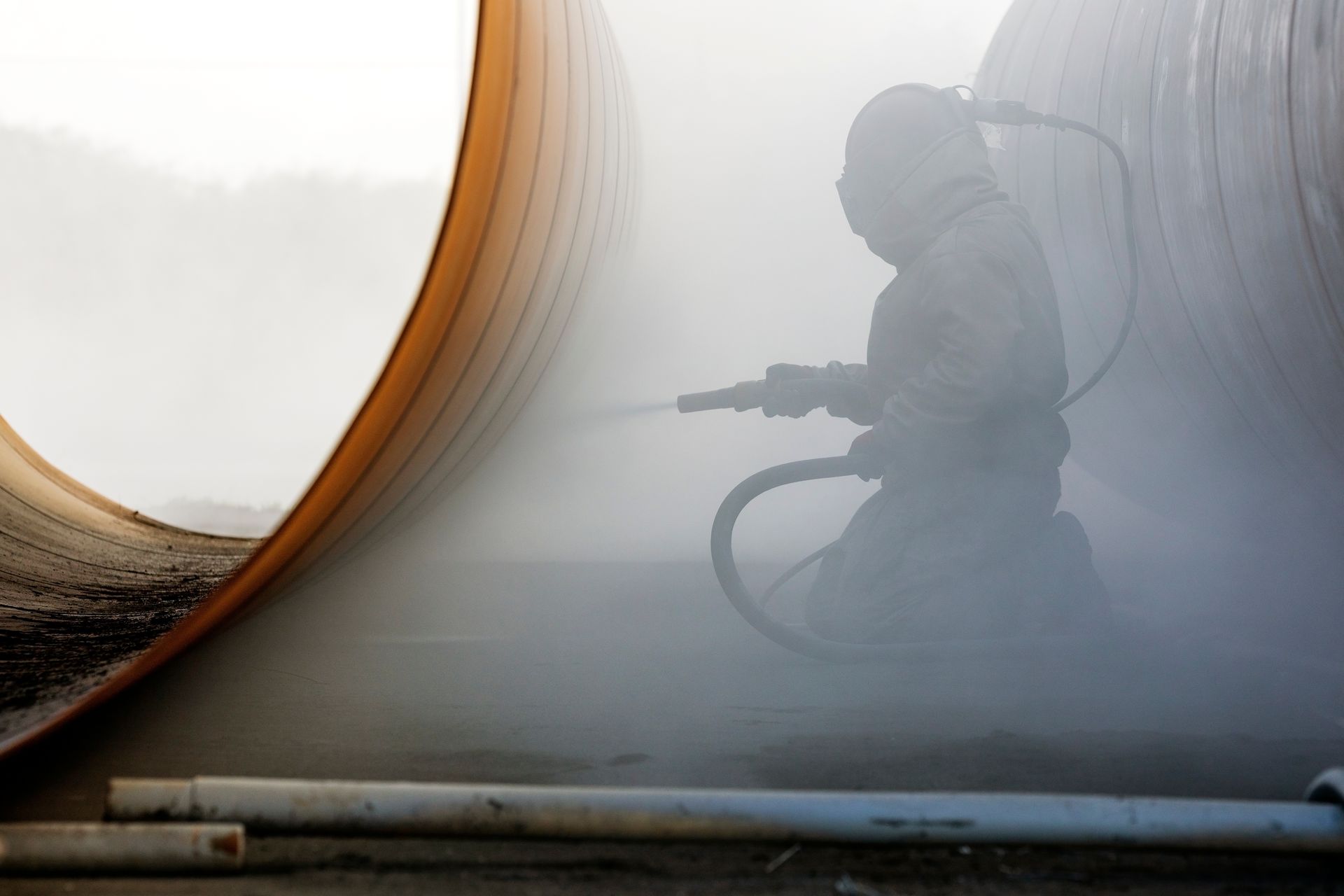
The Hidden Power of Blasting Techniques in Industrial Painting
In industrial painting, it’s easy to focus on the protective coating itself—its thickness, durability, and resistance. But no matter how advanced or expensive a coating may be, it is only as good as the surface it adheres to. That’s where blasting techniques come in.
Blasting techniques are the foundation of proper surface preparation. Whether protecting bridges, offshore rigs, or industrial tanks, using the right blasting techniques ensures coatings adhere correctly, last longer, and perform as designed. Done right, they extend asset life, reduce maintenance costs, and ensure regulatory compliance.
What Are Blasting Techniques?
Blasting techniques refer to the mechanical or abrasive methods used to clean, texture, or prepare a surface—usually metal or concrete—prior to applying a protective coating. The aim is to remove contaminants (rust, scale, old paint, oil) and create a surface profile that promotes strong coating adhesion.
Common blasting techniques include:
- Abrasive Blasting (Grit or Sandblasting)
- Sandblasting, also known as abrasive blasting, is a process that involves propelling a stream of material, typically sand, at high velocity against a surface to clean, etch, or shape it. Traditionally, sand was the primary abrasive material used in this method due to its availability and effectiveness in removing paint, rust, and other contaminants from surfaces like metal, wood, or concrete. However, in the UK, the use of sandblasting has been largely phased out due to significant health and safety concerns associated with the inhalation of crystalline silica dust. Silica is a naturally occurring mineral found in sand, and when sand is blasted at high pressures, it can aerosolise into fine particles that can be easily inhaled. Prolonged exposure to silica dust has been linked to serious respiratory diseases, including silicosis, lung cancer, and other pulmonary disorders.
- In response to these health risks, the UK’s Health and Safety Executive (HSE) has implemented strict regulations regarding the use of silica sand in abrasive blasting. These regulations aim to protect workers from the dangers of exposure, leading to a shift toward alternative materials that do not carry the same health risks. As a result, industries that previously relied on sandblasting have adopted safer methods and materials, such as garnet, glass beads, or even more advanced techniques like wet blasting, which significantly reduces airborne particles. The move away from traditional sandblasting methods reflects a broader commitment to occupational health and safety in the UK, emphasising the importance of worker protection and the use of safer practices in industrial processes.
- Shot Blasting
- Shot blasting is a vital surface preparation technique employed widely across various industries in the UK. This method involves propelling abrasive materials at high velocity onto a substrate, effectively removing contaminants and creating a surface texture suitable for subsequent coating applications. According to ISO 12944, which pertains to the corrosion protection of steel structures, the integrity of surface preparation is critical in ensuring the longevity of protective coatings. The choice of abrasive media, along with the parameters of the shot blasting process, directly impacts the effectiveness of the surface preparation. ISO 8501-1 provides a framework for assessing the quality of the blasted surface, categorising it into grades based on cleanliness and surface roughness. Achieving the appropriate grade outlined in ISO 8501-1 is essential, as it helps in maximising the adhesion of paints and coatings, thereby ensuring optimal performance and durability in various environmental conditions. In the UK, industries such as marine, automotive, and construction rely heavily on shot blasting for preparing components that will endure demanding conditions. Adhering to international standards like ISO 12944 and ISO 8501-1 not only promotes quality assurance but also enhances compliance with environmental regulations, making shot blasting a critical component of modern surface treatment operations.
- Sponge or Soft Media Blasting
- Sponge or soft media blasting is a gentle cleaning method that uses soft sponges or particles to remove contaminants from surfaces without damaging them. This technique is especially useful for restoring delicate or intricate structures, such as historic buildings, fragile equipment, or sensitive electronic components. Benefits of Sponge or Soft Media Blasting include Gentle Yet Effective as It removes contaminants like paint, dirt, and grime without harming the underlying surface. Its also Eco-Friendly Often using biodegradable materials, making it an environmentally friendly option. Its also highly Versatile in its Applications so can be Suitable for various surfaces including wood, metal, stone, and glass. It leaves very Minimal Cleanup and Leaves less waste compared to traditional blasting methods, resulting in decreased cleanup time and costs.
- Applications for soft media blasting include Restoration of historical buildings, Automotive and aircraft refurbishment, Cleaning of delicate machinery and Removal of graffiti and other surface stains. Overall, sponge or soft media blasting is a reliable choice for achieving a clean surface while preserving the integrity of the material being treated.
- Vapour & Slurry Blasting
- Vapour and slurry blasting techniques have gained traction in the UK as effective alternatives to traditional abrasive blasting methods. These processes enhance surface preparation while minimising environmental impact, making them suitable for diverse applications, from metal fabrication to heritage restoration. Vapour blasting, also known as wet blasting, utilises a mixture of water and abrasive media, allowing for a gentler approach compared to dry blasting. The added moisture reduces dust generation, enhancing operator visibility and workplace safety. Furthermore, the combination of water and abrasive particles results in a smooth surface finish, ideal for sensitive substrates such as aluminium or carbon fibre components. Slurry blasting operates on similar principles but focuses on a more viscous mixture of water, abrasive materials, and additives. This method is especially effective in removing heavy contaminants such as rust or old paint while preserving the integrity of the underlying material. The slurry's consistency allows for more controlled application, reducing the risk of substrate damage and improving efficiency.
- Both vapour and slurry blasting are increasingly popular in the UK due to stringent regulatory requirements on environmental sustainability. These methods not only meet these standards but also deliver superior results, making them essential tools in modern surface preparation processes.
* Each method has distinct advantages based on substrate type, site conditions, and coating requirements. Selecting the correct blasting techniques is crucial to project success and industrial coating performance.
Why Surface Preparation and Blasting Techniques Are Non-Negotiable
Applying coatings to unprepared or poorly cleaned surfaces results in:
- Delamination
- Blistering
- Premature corrosion
- Costly failures and rework
According to ISO and SSPC guidance, blasting techniques are the single most influential factor in determining coating performance. Up to 80% of coating failures are linked directly to inadequate surface preparation.
By using verified blasting techniques, asset owners can reduce long-term costs and enhance safety and durability.
Different Blasting Techniques Explained
Abrasive Blasting (Traditional Grit Blasting)
One of the most widely used blasting techniques, this method propels abrasive media (e.g. garnet, steel grit) at high speed to strip contaminants and profile the surface.
- Best for: Corroded steel, mill scale
- Pros: Fast, deep cleaning to SA 2.5 and SA
- Cons: High dust generation, containment often required, particularly when working over water
Shot Blasting
This method uses round metallic beads for a peening effect.
- Best for: Concrete or steel decks
- Pros: Recyclable media
- Cons: Not suitable for angular surface profiles
Sponge Blasting
Combines abrasives in sponge material to reduce rebound and capture debris.
- Best for: Confined or sensitive areas
- Pros: Dust control, surface-friendly
- Cons: Much lower speed than grit blasting
Vapour or Wet Blasting
Adds water to the media stream to suppress dust during blasting, also know as "Slurry" Blasting.
- Best for: Urban or active environments or where dust control is important
- Pros: Dust free working conditions
- Cons: Surfaces must dry before coating unless a moisture tolerant coating product is to be applied
Each of these blasting techniques can be adjusted by changing media, pressure, or moisture content to suit the task at hand.
The Role of Blasting Techniques in Coating Performance
Blasting techniques directly influence three core outcomes: adhesion, cleanliness, and surface profile uniformity.
Adhesion
Anchor surface profiles created by proper blasting techniques give coatings a mechanical grip. This prevents peeling and flaking, especially under UV exposure or chemical attack.
Cleanliness
Blasting removes hidden contaminants—rust, staining etc—which could otherwise cause premature corrosion or certainly reduce the asset lifecycle if a lesser surface preparation method was adopted. Without effective blasting techniques, even the best coatings may fail.
Surface Profile Uniformity
Consistent profiling ensures uniform coating thickness. Variability in the profile leads to over - or under-application and weak points in paint film protection.
Put simply: blasting techniques are the bedrock of protective coating integrity.
Blasting Techniques: Industry Standards and the Role of Coating Inspectors
Industrial coatings are governed by standards that prescribe how blasting techniques should be carried out and verified.
Key Surface Preparation Standards
ISO 8501-1
– Visual Cleanliness
Defines grades of rust removal and preparation levels (Sa1 to Sa3).
ISO 8503
– Surface Profile
Measures surface roughness using comparators or replica tape.
ISO 12944
– Corrosion Protection of Steel Structures
A broad system for selecting coatings and preparation based on environment and durability needs.
SSPC NACE
(now
AMPP)
Society of Protective Coatings in North America although now have merged with NACE National Association of Corrosion Engineers and formed AMPP (Association for Materials Protection & Performance) standards such as SSPC-SP 1-10 guidance for surface prep quality globally recognised.
UK-based certification systems ensuring operatives apply compliant blasting techniques and record results accordingly.
The Role of the Coating Inspector
A certified inspector ensures that blasting techniques meet contract specifications and coating manufacturer requirements.
Pre-Blasting Checks
• Verifies correct media, pressure, equipment, and ambient conditions
Post-Blasting Checks
• Assesses cleanliness (ISO 8501-1) and profile (ISO 8503) amongst others
• Confirms surfaces are ready to coat usually as part of their role
Documentation
• Produces Quality Assurance (QA) and Quality Control (QC) reports for traceability
Communication
• Liaises with applicators and asset owners to avoid costly rework
Inspection ensures blasting techniques are performed properly and are not undermined by poor practice or shortcuts.
Environmental and Safety Considerations for Blasting Techniques
Modern blasting techniques are designed with safety and environmental control in mind. Some of the key elements to consider are:
Dust Control
Wet, vapour, and sponge systems reduce airborne debris.
Media Safety
Silica-free abrasives protect operatives from inhalation risks.
Waste Management
Used media and contaminants are collected and disposed of under environmental legislation.
PPE and Site Safety
Operatives using blasting techniques must wear appropriate gear: blast suits, air-fed helmets, and gloves. Rescue plans are essential for confined or elevated work areas.
Blasting Techniques in Rope Access Environments
Industrial structures such as bridges, offshore platforms, tanks, chimneys, and towers often present access challenges where traditional methods like scaffolding or MEWPs are impractical, time-consuming, or cost-prohibitive. This is where rope access combined with expert blasting techniques becomes a game-changer.
At height or in confined spaces, rope access technicians who are also trained as blasters can safely and efficiently reach areas that would otherwise require extensive temporary works. Their mobility, combined with precision equipment and surface preparation expertise, makes rope access ideal for both routine maintenance and emergency interventions.
Examples of Rope Access Environments:
- Bridges – Blasting undersides without traffic closures
- Tanks & Silos – Internal vertical surface prep
- Wind Turbines – Blasting tower stems and blades
- Offshore Rigs – Corrosion removal in splash zones
- Chimneys – Safe prep at extreme height
Advantages of Rope Access:
- Speed & Flexibility: Teams can be rigged within hours
- Cost-Efficiency: Lower labour and setup costs
- Access Anywhere: Work around curves, flanges, and structural members
- Reduced Risk: Fewer people at height, fewer interfaces
Requirements for Effective Rope Access Blasting
To ensure blasting techniques are effective in rope access settings, several conditions must be met:
• Blasting-specific training and experience for surface preparation operatives
• Use of lightweight and portable blasting equipment suitable for vertical mobility
• Implementation of containment systems to control dust, debris, or rebound at height
• Strict adherence to HSE guidelines, including emergency and rescue planning
At Dangle, we combine technical rigging expertise with specialist blasting techniques training to deliver high-quality surface preparation—no matter how complex the environment.
Common Blasting Techniques Mistakes to Avoid
Even experienced teams can misapply blasting techniques if:
- Media type or pressure is incorrect
- Profiles are inconsistent
- Surfaces aren’t cleaned before coating
- Blasting isn’t completed to the correct specifications (e.g. Sa 2½ instead of Sa 3)
- The coating window post-blasting is missed
At Dangle, we adhere to strict inspection protocols to ensure blasting techniques are done once—and done right.
Learn More About Dangle Rope Access Today
Here at Dangle, we provide a variety of comprehensive inspection, access, coatings, and composite (IACC) industrial services. Our services are available to both the private and public sectors.
We offer high-quality proven solutions that will help reduce maintenance costs in both the long and short-term. We are based in Dundee, Scotland and also have offices based in Edinburgh, along with our newly established training centre in Northern Ireland, Dangle Academy. Due to our company size and structure, we are able to offer a flexible and versatile approach to the way we run our business and the services that we offer our clients. And, as a leading painting company, we’ve worked on several renewable energy projects in the UK, Europe, and the US.
We work with both on and offshore with wind farm operators, and asset owners. For offshore wind farm maintenance, to onshore building maintenance, we can cover both the East and West coasts.
To find out more about how our team can help you
contact us today. Our friendly, professional and helpful team is always on hand to help!